Retronix
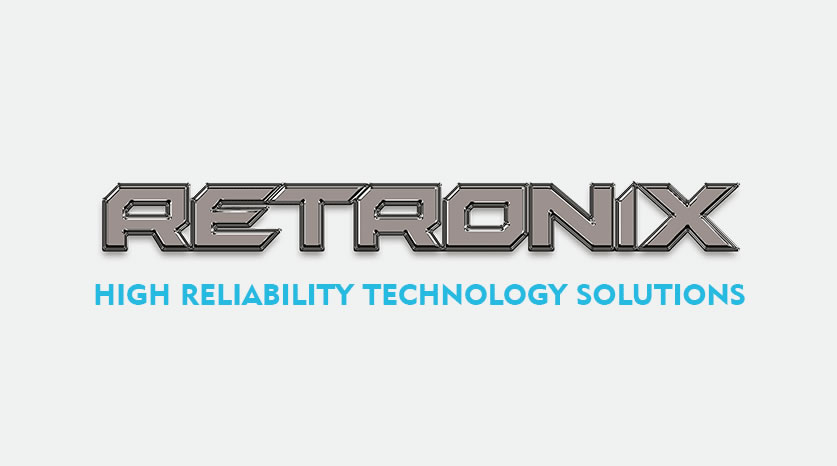
Retronix - Factory Flow Designer
Design factory flows, rules and logic without code.
Challenge:
Our client, an electronic manufacturing factory, was struggling with a flexible way to design and manage factory flows through their system. The time taken to change the flows and process logic was causing inefficiencies and they were struggling to offer their customers the levels of flexibility and customization they needed.
Large customers like this frequently have very detailed requirements and specifications for processes such as re-balling and re-tinning. They needed to find a way to improve the design and implementation of these factory flows that was near instant and could be customized to their clients' exact requirements. This also needed to be demonstrated to clients during factory audits.
Solution:
Working closely with our client, we completed a comprehensive analysis of the requirements for such a solution. The following essential requirements were identified in this process:
- The design and modifications of factory flows needs to be 100% flexible without having to re-code parts of the system (i.e. no coding for any changes)
- Tasks within any flow may have references such as client specifications, diagrams or other documentation that a factory operation may need to review during the factory process. These need to be configurable during the design process.
- Task within any flow may have a number of required outputs such as consumable verification, form completion, inspection confirmations and photographs. These need to be configurable during the design process.
- Task routes need to be able to take on complex paths with the ability to make tasks optional.
Results:
Through our partnership with our client, we were able to develop an ultra-flexible web-based system that allowed them to create and manage complex factory flows in minutes. These 'task flows' cleanly integrate with the rest of the factory management system and are now used as the basis for a fully auditable factory flow from arrival in the factory to packing and packaging.
Our client is able to provide clear visibility to their clients which has significantly improved the efficiency of audits and helped to build trust. The system led to a significant decrease in operator mistakes, which in turn led to increased productivity and reduced costs.
All task flow changes can now be made in real-time allowing factory managers to identify issues as they happen and take corrective action quickly. This helped to further improve efficiency and reduce downtime.
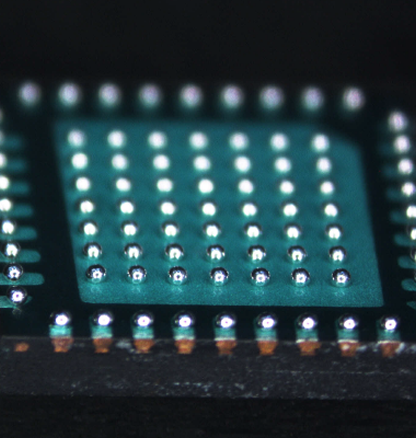
Categories
- Location Scotland, UK
- Completed Date June 2023